Green Hydrogen Microgrids: A Techno-Economic Assessment to 2030
- maktinta
- Mar 18
- 19 min read
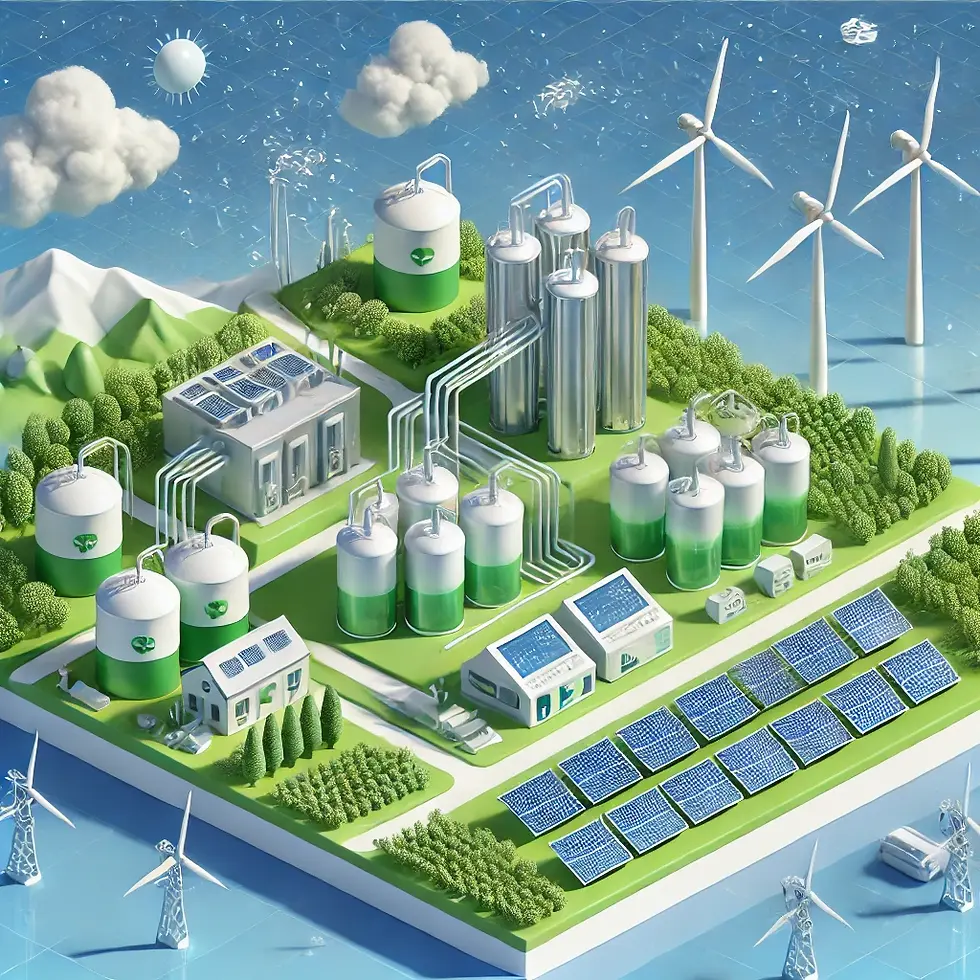
Microgrids powered by green hydrogen are emerging as a potential solution for clean, resilient energy in small-scale applications like data centers, mega charging stations and isolated communities. These systems combine renewable power (solar, wind, or hybrids) with electrolyzers and fuel cells to produce and use hydrogen on-site as an energy storage medium. This blog post assesses the techno-economics of such setups – focusing on the U.S. market with comparisons globally – and projects cost trends to 2030. We’ll break down the cost to generate green power, the cost to produce green hydrogen, the energy efficiency trade-offs, and the financial viability (including sensitivity analyses). Finally, we compare U.S. cost structures with global markets and summarize key insights.
1. Cost of Producing 1 kW of Green Power (Solar/Wind)
For a microgrid, the first step is generating renewable electricity. The cost to install and run 1 kW of solar or wind capacity includes land, equipment (panels, turbines, inverters), permitting, installation labor, and ongoing maintenance, as well as performance degradation over ~20 years. These factors determine the Levelized Cost Of Electricity (LCOE) from the renewable source:
Solar PV: In the U.S., small-scale solar PV installations typically cost on the order of $1,000–$2,000 per kW of capacity (higher than utility-scale due to scale and balance-of-system costs). Over 20 years (assuming ~0.5% output degradation annually), this translates to an LCOE in the range of $0.05–$0.10 per kWh for good solar resources. Globally, costs have dropped significantly – the 2022 average LCOE for utility-scale solar was just $0.044/kWh (about $44/MWh). However, microgrid-scale projects may see somewhat higher costs due to smaller size and added battery/storage integration. Land requirements for solar are modest (about 2–3 acres per MW) and often the panels can be sited on rooftops or unused land, minimizing land cost impact. Yearly maintenance (panel cleaning, inverter replacements) is relatively low (on the order of $10–$20 per kW-year).
Wind: Onshore wind turbines have a higher upfront cost per kW but also a higher capacity factor (they generate power a larger fraction of the time). Installing 1 kW of wind capacity might cost roughly $1,500–$2,500. Over 20 years, LCOEs for onshore wind can be as low as $0.03–$0.05/kWh at good U.S. sites (the global average in 2022 was $0.033/kWh). Small community wind projects may incur extra costs for permitting (e.g. environmental assessments, local zoning) and maintenance (servicing turbines), but benefit from higher energy output in windy regions. Wind requires more land space (and setback distance) per kW than solar, but the land (often farmland) can usually still be used for other purposes.
Hybrid (Solar + Wind): Combining solar and wind can yield more consistent power output, reducing the need for oversized capacity or storage. For example, solar produces during the day, wind often picks up at night or different seasons – a complementary profile. The cost of a hybrid 1 kW system would be a weighted combination of both; often one invests in both sources so that for each 1 kW of load, you might install e.g. 1 kW solar and 1 kW wind. While this doubles the capacity, it ensures reliability and better utilization of equipment. Hybrid systems can thus lower the effective cost per kWh delivered by improving the capacity factor of the renewable mix. Still, they will incur the capital costs of both sets of equipment and potentially higher integration costs (controls to manage two generation sources).
Summary: For a microgrid, expect roughly $1,000–$2,000 per kW in upfront costs for renewables, yielding green power at $0.05–$0.10 per kWh in the U.S. (assuming favorable conditions). By 2030, incremental improvements (cheaper solar modules, more efficient wind turbines) could push these costs down further. The U.S. has some of the lowest renewable costs globally, thanks to abundant land and resources, whereas regions like Europe have higher costs (e.g. solar LCOE in the EU can be higher due to less sun and higher land costs). Globally though, the trend is downward – renewables are now often the cheapest source of new power, which bodes well for green hydrogen’s input costs.
2. Cost of Producing Green Hydrogen
Turning renewable electricity into hydrogen adds another stack of costs. Green hydrogen is produced via electrolysis – using an electrolyzer to split water into hydrogen and oxygen – and then typically needs compression, cooling, storage, and possibly transportation if not used on-site. We break down the key cost components to produce 1 kilogram of H₂ (which contains about 33.3 kWh of energy):
Electrolyzer Equipment & Installation: This is the capital cost of the electrolyzer plant per kW of hydrogen production capacity. Current electrolyzers (PEM or alkaline) cost around $500–$1,000 per kW (though DOE targets <$300/kW by 2030). Amortized over its life (20 years at a certain utilization), the capital contributes roughly $0.11–$0.55 per kg H₂. This range reflects economies of scale: large projects can approach the low end, whereas a small-scale unit in a microgrid might be on the higher end of cost. Land and permitting for the electrolyzer are usually a minor portion but can add some cost (installing an electrolyzer next to a data center or in a community might require safety buffers and compliance with hydrogen safety standards).
Fixed O&M: The electrolyzer and related hydrogen equipment require maintenance (replacing membranes, filters, monitoring systems) and incur some fixed operating costs. These costs add about $0.12–$0.24 per kg in a typical setup. Regular maintenance is crucial to keep efficiency from degrading year-over-year – electrolyzers may slowly lose efficiency or capacity, which we account for in lifecycle costs.
Electricity Supply: The largest cost driver for green hydrogen is the electricity used in electrolysis. At today’s electrolyzer efficiency (around 70–80%), it takes roughly 50–60 kWh of electricity to produce 1 kg of H₂. If renewable power costs $0.04/kWh (unsubsidized, a representative cost for wind/solar in the U.S.), then the electricity expense per kg is about $2.00 (50 kWh × $0.04) – this corresponds to $1.89–$2.16/kg in our example. In reality, a microgrid might sometimes use its “excess” solar/wind to feed the electrolyzer (which could be seen as $0 marginal cost if it would otherwise be curtailed), but for most economic analysis we treat it as a cost since that energy has value. If grid power is used as backup, its price will affect hydrogen cost too. By 2030, if renewables get even cheaper (say $0.02–$0.03/kWh in best cases), this electricity cost could drop proportionally – but it will still be the dominant factor in H₂ cost.
Compression & Cooling: Freshly electrolyzed hydrogen is at low pressure and needs to be compressed (or liquefied) for storage. For microgrid fuel cell use, H₂ is often stored as a compressed gas at 200–700 bar. Compressing 1 kg H₂ to 350–700 bar consumes about 2–6 kWh of electricity (5–15% of the hydrogen’s energy content) and requires robust compressor equipment. This adds on the order of $0.08–$0.24 per kg in cost (including both capital and energy for compression). Cooling may be needed if using liquid hydrogen, but that’s unlikely in small systems due to complexity. Most microgrids will stick with compressed gas storage for simplicity, despite the energy penalty for compression.
Storage Tanks: Storing hydrogen safely (often in high-pressure cylinders or tanks) entails capital cost but usually this is accounted for in project capex rather than per-kg. However, if the system must store large quantities (e.g. to cover many days of autonomy for a remote community), storage tank costs can be significant and sometimes a limiting factor. (In one sensitivity analysis, hydrogen tank cost was found to dominate 42% of lifecycle cost when large storage was needed in a microgrid. For short-duration backup (like a data center that needs 48 hours of backup), storage costs are manageable, but for seasonal storage, they’d be much higher.
Transport (if applicable): In our microgrid context, we assume hydrogen is produced and used on-site, so transportation cost is minimal. If hydrogen needed to be trucked in or piped from elsewhere, that would add cost. (For perspective, building dedicated H₂ pipelines is extremely expensive – estimated $2.3–$4.5 million per km. This is why most green hydrogen projects aim to use it locally or blend into existing gas pipes. Putting it all together, a recent analysis found that even under optimistic assumptions, green hydrogen costs are unlikely to fall much below $3 per kg (excluding any battery storage costs). When accounting for the need to buffer renewable intermittency (e.g. adding batteries or oversizing capacity), the effective hydrogen cost could range from $3.6 up to $8+ per kg in small-scale setups. We can illustrate an example breakdown per 1 kg H₂:
Electrolyzer Capex: $0.3/kg (mid-range assumption)
Electrolyzer O&M: $0.2/kg
Renewable electricity: $2.0/kg (50 kWh @ $0.04)
Transmission/Integration: $0.5/kg (if pulling from grid or distant wind farm)
Compression & misc.: $0.15/kg
Subtotal: ≈ $3.15/kg (not including storage buffering)
Intermittency buffer: +$1–$3/kg (if using batteries or overbuilding renewables)
Total: roughly $4–$6/kg for fully green hydrogen at small scale.
Using latest numbers available (2024), green H₂ produced via electrolysis typically costs about $5/kg in the U.S. , whereas gray hydrogen from natural gas reforming (without carbon capture) costs only $1–$1.50/kg. The U.S. Department of Energy’s Hydrogen Earthshot seeks to cut green H₂ cost to $1/kg by 2030, an 80% reduction. Achieving this is extremely ambitious – it would likely require ultra-cheap electricity (on the order of $0.005/kWh or $5/MWh) and new efficient technologies. In reality, by 2030 experts project green hydrogen in favorable locations could drop to around $2/kg. U.S. policy is trying to bridge the gap: the 2022 Inflation Reduction Act provides a $3/kg production tax credit for green hydrogen, which effectively subsidizes current $5/kg costs down to ~$2/kg. In Europe, where electricity is pricier, current green H₂ costs are about $4.5–$6/kg. Regions with cheap renewable power (e.g. the Middle East, parts of Africa or Australia) aim to produce green hydrogen for $1–$2/kg by 2030 for export, leveraging low land and solar costs. But for our context of small-scale, on-site hydrogen usage, costs will tend to be higher than these large-scale projections due to lower economies of scale.
3. Energy Analysis: Input vs. Output Efficiency (Hydrogen’s Round-Trip)
Hydrogen is often described as an energy storage medium or carrier, not an energy source – and a fundamental challenge is the efficiency of the round-trip from electricity to H₂ and back to electricity. In a microgrid setup, one would use surplus renewable electricity to produce hydrogen (store energy), then later use that hydrogen in a fuel cell or generator to make electricity when needed. It’s crucial to understand how many kW of electricity are invested in making hydrogen vs how many kW are ultimately delivered from it.
From a pure energy standpoint, there is a significant loss in the conversion process:
Electrolysis Efficiency: Modern electrolyzers are ~70–80% efficient. This means if you put in 100 kWh of electricity, you get at most about 80 kWh worth of chemical energy in hydrogen (and 20 kWh are lost as heat and other losses). Put another way, producing 1 kg of H₂ (33.3 kWh of energy in lower heating value) requires ~50–60 kWh of electricity input. Any degradation in electrolyzer performance over time or suboptimal operating conditions (part-load efficiency losses) will further reduce this efficiency.
Compression and Storage Losses: As mentioned, compressing the hydrogen uses additional energy (roughly 5–10% of the H₂ energy). If we had 80 kWh of hydrogen energy after electrolysis, we might spend ~4–8 kWh to compress it for storage, leaving ~72–76 kWh usable in the tank. There are also some boil-off or leakage losses if stored long-term (negligible for short durations but can accumulate over months).
Fuel Cell / Generation Efficiency: To use the stored hydrogen, it’s typically fed into a fuel cell (or sometimes a combustion generator or turbine) to convert back to electricity. Fuel cells (PEM type) are around 50–60% efficient in converting hydrogen’s energy to electricity. Combusting hydrogen in an engine or turbine is usually less efficient (~30–40%) unless it’s a high-efficiency turbine. Assuming a fuel cell at 50%, our ~75 kWh of hydrogen from above yields only about 37 kWh of electricity output to the load. If using a generator at ~35% efficiency, it’d be ~26 kWh out. Overall, the round-trip efficiency from electricity → hydrogen → electricity is roughly 30–40% for a fuel cell system. In other words, for every 1 kWh put into making hydrogen, you might get only 0.3–0.4 kWh back in useful electricity later. This aligns with a simple energy return calculation: the energy content in the hydrogen is only ~60% of what you used to make it, and then you lose about half again in the fuel cell. An analysis by the Manhattan Institute starkly points out that “the useful energy contained in hydrogen produced via electrolysis is, at best, just over 60% of the energy required to manufacture it”(that is just chemical energy in H₂ vs input, not even counting conversion back to power). Thus, hydrogen has an energy return on investment (EROI) well below 1 – you get <0.6 units of energy for every 1 unit you put in– whereas conventional fuels or batteries have higher returns (fossil fuels and nuclear have EROIs > 1, meaning more energy out than in, at least at the point of use. This inefficiency is a key reason some analysts call green hydrogen a “boondoggle” for energy storage, since by the laws of thermodynamics you inherently lose a lot of the renewable energy you started with.
From a microgrid perspective, this means to guarantee 1 kW of power output from hydrogen, one must have generated roughly 2.5–3 kW of extra renewable power earlier to charge the system (not to mention the capital cost of the equipment to do so). If instead that extra renewable power could be stored in a battery (with round-trip efficiency 85–90%) or used directly, it might be utilized more effectively. Why use hydrogen then?
The main reason is storage duration and energy density: batteries are great for hours, maybe a day, but for multi-day or seasonal gaps, batteries become prohibitively expensive or impractical, whereas hydrogen can store large amounts of energy for long durations. Thus, despite the efficiency penalty, green hydrogen can make sense for long-term storage or when fuel portability is needed. In a data center backup scenario, for instance, efficiency is less critical than reliability during a 48-hour outage – if hydrogen can keep servers online with zero emissions, it may justify the energy losses. (Indeed, a Microsoft data center pilot recently ran 48 hours on hydrogen fuel cells, achieving 99.999% uptime in the test.
In summary, the energy analysis underscores that every kW used to produce hydrogen yields only ~0.3–0.4 kW in the end (for electricity output). This low efficiency means the economics must compensate through either very cheap input power or very high value of the output power (e.g. avoiding a costly outage or diesel generator use).
4. Financial and Sensitivity Analysis (20-Year Viability)
To evaluate if a green hydrogen microgrid makes financial sense, we conduct a project-style financial analysis over a 20-year lifespan. This involves calculating capital expenditures (CAPEX), annual operating costs (OPEX), and potential revenues or savings, then computing metrics like Net Present Value (NPV), Internal Rate of Return (IRR), or Levelized Cost of Energy (LCOE for the delivered electricity). Key financial assumptions include the cost of capital (interest/discount rates) and any incentives.
Base Financial Assumptions (Current): Let’s assume a project financing with a mix of debt and equity. In the U.S. today, interest rates for energy projects might be around 5–7% for debt, and equity investors might target ~8–12% returns, giving a weighted average cost of capital (WACC) on the order of 6–8%. We’ll use a discount rate ~7% for NPV calculations, reflecting the risk and the fact that hydrogen is a nascent tech (possibly higher than the ~5–6% used for mature renewables). We also factor in degradation of the solar/wind output (~0.5%/yr) and electrolyzer/fuel cell performance decline over time, as this affects output and maintenance costs.
Cash Flows: In year 0, a large CAPEX is incurred for purchasing and installing solar/wind, the electrolyzer system, hydrogen storage, and fuel cells. For example, a small community microgrid might require $6-$8 million upfront for a few MW (see our Blog – The Shift to Solar Powered Data Centers) of renewables and hydrogen infrastructure. Operating costs each year include: maintenance of solar/wind (maybe 1–2% of their capital cost annually), maintenance of electrolyzer and fuel cell, the cost of any electricity purchased from the grid (if needed), and general microgrid operations. On the revenue side, if the microgrid is displacing electricity that would otherwise be bought from the utility, each kWh generated has a value equal to the retail rate avoided. In a data center’s case, the “revenue” might be avoiding the cost of a power outage (which can be very high), or perhaps earnings from providing grid services (some data centers could sell excess power or provide demand response). However, most often we evaluate in terms of cost savings rather than direct revenue, unless the hydrogen is sold as a commodity.
Levelized Cost of Energy: One way to gauge viability is to compute the effective cost per kWh of electricity delivered by the hydrogen microgrid over 20 years, and compare it to alternatives (like diesel generators, batteries, or grid power). Given the inefficiencies and costs we outlined, this LCOE for hydrogen-based power tends to be high. A recent study in Spain analyzed a campus microgrid and found that at current costs, the breakeven electricity price would need to be about €0.61 per kWh (i.e. $0.65/kWh) for a hydrogen-priority system to be profitable. In other words, if the microgrid’s output is valued at $0.65/kWh or higher, the project breaks even; anything less and it loses money. For context, normal retail electricity is around $0.10–$0.30/kWh, so $0.65 is extremely high. If hydrogen technology costs drop dramatically (100% cost reduction in that study’s scenario), the breakeven price fell to ~€0.16/kWh– better but still above typical rates. A battery-centric approach was slightly cheaper (requiring ~€0.40/kWh at current costs), highlighting that even with optimistic cost declines, hydrogen storage is currently more expensive than battery storage for short-duration needs.
Economic Viability: In the U.S., one could argue a hydrogen microgrid might make financial sense in niche cases: for example, if a remote community currently relies on diesel generators at $0.50/kWh or more, a renewable+hydrogen system that delivers power at $0.40–$0.50/kWh could compete. Likewise, data centers paying for both electricity and diesel backup might justify a premium for a cleaner solution. But generally, without incentives, the pure market case is tough. Subsidies and credits can tilt the economics – the $3/kg hydrogen production credit (IRA) is effectively a $0.09/kWh credit on the hydrogen’s energy (since $3/kg ≈ $91/MWh energy content. This helps reduce operating cost significantly. Additionally, low-interest “green loans” or government grants (like the DOE funding for hydrogen hubs) reduce the effective capital cost. In our Microsoft data center example, the project was partially funded by DOE’s H2@Scale initiative. Such support can improve the project IRR from negative to positive territory.
Sensitivity Analysis: It’s instructive to see which variables most impact the economics. In a tornado diagram (a bar chart showing the effect of varying one parameter at a time on the NPV or LCOE), typically the cost of electricity for electrolysis is the #1 driver.
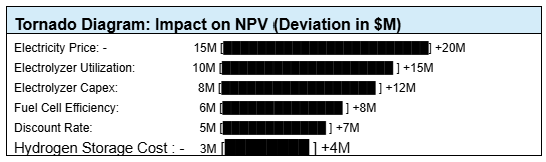
Since power supply makes up ~50–70% of hydrogen cost, changes in renewable energy cost or availability have a huge effect. For instance, if our solar/wind LCOE is $0.04/kWh vs $0.08/kWh, it could double the hydrogen cost per kg, which then cascades into the cost of delivered electricity. The utilization rate of the electrolyzer and fuel cell is another big factor: these are expensive assets – if they sit idle many hours (due to either not enough excess power or not enough demand to use hydrogen), the effective cost per kg goes up. Running the system at a higher capacity factor spreads out capex over more output. Therefore, assumptions about how often the microgrid will need to draw on the hydrogen (e.g. only during occasional outages, or daily load shifting?) can swing the economics.
Other sensitive parameters include: Electrolyzer capital cost (expected to drop with scale, but if it stays high, it’s a big cost chunk), fuel cell cost and efficiency (better efficiency means more kWh out per kg H₂, effectively lowering cost per kWh delivered), hydrogen storage cost (if long autonomy is required, the tank size and cost can become a major contributor), and the discount rate itself (a higher rate penalizes the long-term payback of fuel savings). For example, even if technology costs fall, a high interest rate can kill project economics by front-loading the burden of capital. Conversely, low-interest financing or leasing models could make it easier to justify the investment.
To highlight an example: one DOE analysis of hydrogen production showed its cost was most sensitive to the electricity price and capacity factor, followed by electrolyzer capital cost and efficiency – these formed the longest bars on a tornado chart. Another study noted that a 100% reduction in hydrogen system costs (i.e., in a hypothetical future where electrolyzers and fuel cells are nearly free) would still require electricity around $0.16/kWh to break even, whereas a more modest cost drop combined with high electricity price (like islands paying $0.50/kWh for diesel power) could make systems viable sooner. The takeaway is that cheap clean electricity (or high incumbent energy prices) is the linchpin for green hydrogen microgrids to make financial sense. All other improvements, while helpful, don’t overcome expensive energy input. As one skeptic put it, even at 95% electrolyzer efficiency, you’d need virtually free power (~$5/MWh) to hit $1/kg H₂– a price far below even the O&M cost of wind/solar farms. This emphasizes how challenging the economics are without game-changing innovation or market conditions.
For a 20-year NPV analysis, typically current scenarios show a negative NPV (i.e. costs outweigh benefits) for green hydrogen microgrids under normal electricity price conditions. However, if we include external factors like carbon pricing (valuing the CO₂ avoided), improved resiliency (preventing costly outages), or future proofing against fuel price volatility, the value proposition can improve. A sensitivity graph might show that with a $50/ton carbon credit and $0.03/kWh renewables, the NPV becomes positive, for instance. Project developers will crunch these numbers case-by-case.
In summary, the financial analysis suggests that as of now, green hydrogen microgrids often need subsidies or special conditions to be financially viable, but improvements toward 2030 (cheaper electrolyzers, higher fuel costs for alternatives, and policy support) could tip certain scenarios into profitability. It’s a high upfront investment for long-term gains, and very sensitive to key drivers like power cost and utilization rates.
5. Research & Market Comparison: U.S. vs Global Outlook
There is a rich body of research examining green hydrogen systems. On one end, we have critical perspectives like the Manhattan Institute’s “Green Hydrogen: A Multibillion-Dollar Energy Boondoggle”, which argues that hydrogen for energy storage is inherently inefficient and uneconomic without massive subsidies. This viewpoint highlights fundamental challenges (low EROI, high costs) and suggests resources might be better spent on other solutions (they even note a $3/kg subsidy is equivalent to subsidizing electricity at $91/MWh, far above market prices. On the other end, numerous academic and industry studies explore how hydrogen can be integrated into microgrids and what future cost reductions might make it viable.
For instance, researchers have analyzed hybrid solar-hydrogen systems in various countries: a 2020 Korean study investigated a renewable-based hydrogen production system and performed a techno-economic analysis (Green hydrogen in Korea faced high costs due to expensive electricity, needing further innovation). In Europe, a study of a Spanish campus microgrid (mentioned above) explicitly calculated the required electricity price for profitability with hydrogen vs batteries. Another study in the UAE looked at a commercial-building microgrid with hydrogen storage, finding that current costs lead to very high LCOE, but with future cost declines and high sunlight, the concept could approach viability. These studies generally conclude that today’s economics are challenging, but they map out scenarios (cost decline trajectories, technology improvements, higher carbon prices) under which hydrogen-based microgrids could become competitive by or beyond 2030.
United States: The U.S. is aggressively funding hydrogen R&D and deployment. Aside from the $3/kg production credit, the Department of Energy announced $7 billion for regional hydrogen hubs, some of which will involve green hydrogen for power applications. U.S. cost structure benefits from relatively cheap renewable energy (e.g. Midwest wind or Southwestern solar at 2–4 ¢/kWh) which can lower hydrogen production cost. However, the U.S. also has very cheap natural gas and established infrastructure, meaning the opportunity cost of switching to hydrogen is high in many cases (gray hydrogen or natural gas power is inexpensive). The niche where U.S. hydrogen microgrids are gaining traction is in critical backup power (data centers, military bases) and remote off-grid sites (e.g. microgrids in Alaska or Hawaii where diesel is costly). The example of Microsoft’s data center in Wyoming demonstrates U.S. companies exploring hydrogen for clean backup. Similarly, several utilities are piloting hydrogen blending in microgrids to enhance resiliency (combining batteries, hydrogen fuel cells, and renewables). The U.S. market by 2030 is expected to focus on these high-value, subsidy-assisted use cases rather than bulk grid storage. Essentially, the U.S. strategy is to drive down the cost through scale and innovation (aiming for that $1/kg goal) and use generous incentives to kickstart projects in the meantime.
Europe and Global: Europe has taken a lead in green hydrogen commitment, partly driven by climate goals and the need to reduce reliance on imported fossil fuels. Electricity prices are higher in Europe (especially after 2022 energy crises), which paradoxically makes green hydrogen somewhat more competitive against grid power – but also harder to produce cheaply. European projects often emphasize power-to-gas-to-power for remote islands (e.g. Orkney in Scotland has a hydrogen ferry and microgrid pilot) or for replacing diesel in remote communities. The Scottish HydroGlen project in the Highlands, for example, is building a farm-scale hydrogen microgrid with on-site wind and solar to fully meet local energy needs as a demo. Europe is also investing in infrastructure for future hydrogen trade (the proposed 53,000 km “European Hydrogen Backbone” pipeline network, indicating a long-term bet that hydrogen will become widespread. However, current costs in Europe ( $5–6/kg H₂, higher than U.S.) mean most projects rely on government funding (e.g. the Just Transition Fund in Scotland gave £6.2M to HydroGlen in 2022). By 2030, Europe hopes to have scaled electrolyzer manufacturing and achieved lower costs, but it may still lag the U.S. in raw production cost due to energy prices.
Other global markets: Japan and South Korea are investing in fuel cells and import infrastructure, since they lack cheap renewables domestically. Their focus is often on fuel cells for buildings and data centers (e.g. Japan’s ENE-FARM for homes, or backup power fuel cells) and on securing green ammonia/hydrogen imports from abroad. Australia and the Middle East plan to be suppliers – they have abundant solar/wind and land, so they target producing green hydrogen at <$2/kg for export. While these exports might go to industry or transport, they could also feed remote microgrids in the region (for example, mining sites in Australia using solar + hydrogen storage instead of diesel). Developing regions with no grid could leapfrog with renewable hydrogen microgrids if costs come down; for now, most are opting for solar + batteries (cheaper and simpler).
In summary, the U.S. microgrid hydrogen market is currently driven by incentives and specific use-cases (where reliability and decarbonization justify the cost), whereas globally, some regions face even higher costs (Europe) while others see hydrogen as a future cheap resource (MENA, Australia) but are early in development. By 2030, we expect costs to converge downward somewhat: learning-by-doing and scale should reduce electrolyzer costs, and hopefully $/kg falls into the $2–$4 range broadly (without subsidy) if all goes well. The U.S. may achieve effective costs ~$1–2/kg with the help of subsidies, potentially making green hydrogen viable for more microgrid projects. Yet, as multiple studies and the Manhattan Institute piece highlight, there will remain a gap between hydrogen and alternatives (like direct renewable usage or batteries) in many scenarios unless that gap is closed by policy or unique needs.
In Summary: Can green hydrogen cost-effectively power microgrids for data centers and communities? Not quite yet in most cases – but it’s on the horizon. Our analysis shows that while the technology works (e.g. 48-hour fuel cell backup of a data center was successfully demonstrated, the economics are the crux. Producing 1 kW of reliable green power via hydrogen requires a substantial investment in renewables and equipment, and due to inefficiencies, the net energy return is only about 30–40%. Current costs to produce green hydrogen (~$5/kg in the U.S., $4.5–$6 globally) translate to a delivered electricity cost far above normal power prices. Over a 20-year project life, most green H₂ microgrids would lose money without incentives or extraordinary circumstances, according to multiple studies.
However, the trajectory toward 2030 is favorable: renewable energy keeps getting cheaper, electrolyzers are expected to scale up and drop in price, and strong policies (especially in the U.S. with tax credits and funding) are buying down the costs. If wind and solar can provide ultra-low-cost excess power and if electrolyzer efficiencies improve, green hydrogen for microgrids can approach viability. For example, with electricity at $0.02/kWh and a $3/kg credit, hydrogen at ~$2/kg is achievable, which could make remote microgrids competitive with diesel. Furthermore, the value of carbon-free, resilient power is rising – data center operators and communities are placing premiums on sustainability and reliability. This value (avoidance of CO₂ or outages) often isn’t fully captured in simple LCOE calculations but can tip decision-making.
In practical terms, hybrid solutions may emerge as the optimal approach by 2030: using batteries for short-term needs and green hydrogen for longer-term backup. Sensitivity analyses indicate that no single silver bullet will magically make hydrogen cheap; rather, incremental improvements across the board (cheaper kit, cheaper power, better utilization, financing, and continued subsidies or carbon pricing) will collectively bring costs down. It’s also likely that early deployments will continue in high-cost energy environments or mission-critical applications – proving grounds where hydrogen doesn’t have to beat a $0.10/kWh grid, just a $0.50/kWh diesel or a priceless outage.
In conclusion, green hydrogen microgrids today are a technically feasible but economically challenging proposition. The U.S. is pushing hard with investments to change that equation by 2030, aiming for small-scale systems that could power a neighborhood or data center cleanly and reliably. Globally, interest is high, but cost structures vary – some regions forge ahead despite costs (for climate goals), others wait for cheaper tech. Keep an eye on the next few years: as pilot projects multiply and manufacturing scales up, we’ll get a clearer picture of whether green hydrogen can shed its label as a “boondoggle” and become a mainstream solution, or whether it will remain a niche player for special cases. Either way, the pursuit of green hydrogen is already yielding innovations and driving down costs that will benefit the broader clean energy transition, in microgrids and beyond.
Comments